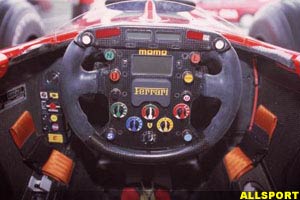
Every bit of a Formula One cockpit not occupied by the driver is crammed tight with technology.
- Buttons: The carbon fibre steering wheel houses controls for the communication radio, the setting of the differential (to change handling characteristics), the fuel mapping (to change the power/economy compromise), the pit lane speed limiter, and the traction and launch control.
- Controls: Behind the steering wheel are controls for the clutch – needed only to get the car moving when launch control isn’t being used – and the gear change. The driver uses a flipper switch on one side of the wheel to make downchanges and one on the other side of the wheel to make upchanges. Normally the gear changes are made automatically – making these controls redundant – but in some situations, a driver may prefer to change gears manually or may be forced to because of technical glitches.
- Instruments: In terms of instrumentation, the cockpit display is quite bare. Small digital read-outs tell the driver engine revs, engine temperatures, minimum corner speeds, and instant lap times.
- Pedals: The cars have only two pedals: a throttle on the right and brake on the left. Most Formula One drivers brake with their left foot.
- Seat: The driver’s seat is moulded to his own particular shape.